niponica is a web magazine that introduces modern Japan to people all over the world.
2013 No.11
To read the e-book you need to have JavaScript enabled in your browser and a free Flash Player plug-in from Adobe Systems Inc. installed.
Strolling Japan

Okinawa, Islands of Cloth
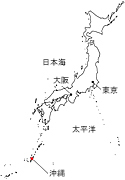
Photos by Ito Chiharu Map by Oguro Kenji

Fabrics crafted on the main Okinawa island. From left, Shuri-ori, Yomitansan hana-ori, and Ryukyu gasuri. (Collaboration: Ryuka)
Located at the southwestern tip of Japan, the Okinawa islands are known for tourism and resorts. Blessed with a warm climate year-round that contrasts starkly with the extremes of heat and cold in the rest of the country, the islands are one of Japan's most popular destinations. A lesser-known aspect of Okinawa is its rich tradition of dyeing and weaving. There are many high-quality, lightweight hemp and silk fabrics in Japan, but a culture of light fabrics that are cool to wear is deeply engrained in Okinawa thanks to the region's climate.
Home of traditional bashofu cloth, the Kijoka Ogimi-son region is located in the northern part of the main Okinawa island. To those living in hot and humid Okinawa, this light and airy fabric is essential to staying cool. Bashofu is woven from the fibers of a large plant called ito-basho that looks something like a banana tree. Even today, the process of making bashofu cloth involves 23 different steps, all carried out by hand, beginning with planting and harvesting the ito-basho, continuing through the u-umi process ( joining the stalk fibers to make a continuous length of thread), and finally ending with weaving the cloth. Every part of this process, from the raw materials to the techniques used, is unique to Okinawa.
A skilled bashofu artisan, Taira Toshiko is pivotal in today's efforts to revive bashofu techniques. She took us through the u-umi stage of creating bashofu. This stage has a great impact on the texture of the finished cloth and is therefore the process that requires the most highly skilled and experienced artisans. Taira's hands move faster than the eye can see, dividing the ito-basho fibers into countless thin threads. This is truly a skill that can only be mastered with many years of experience.
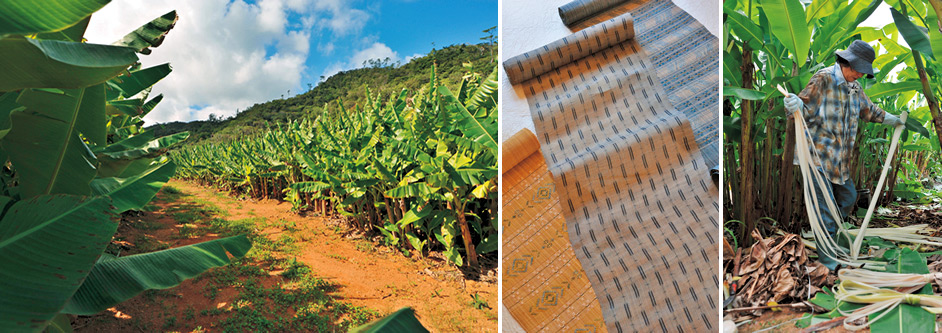
Left: Fields of ito-basho provide the raw materials for bashofu.
Center: Bashofu looks as cool as it feels.
Right: U-hagi, harvesting the ito-basho fibers.
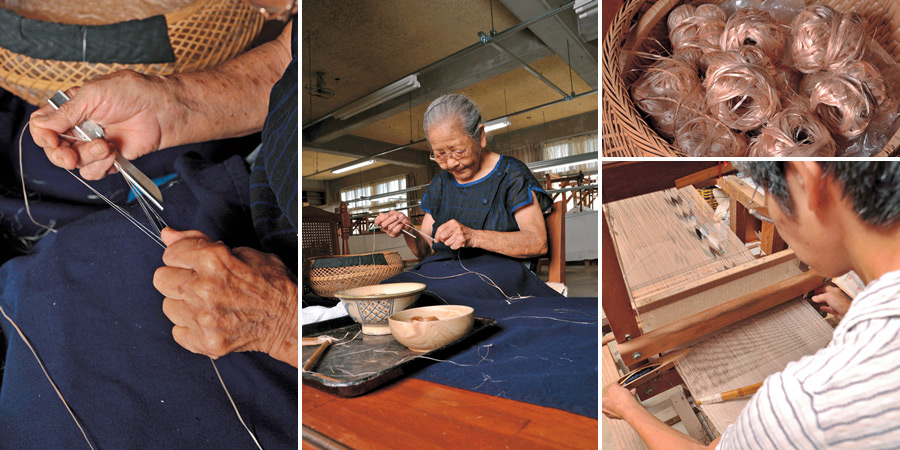
Left: U-umi, making thread from ito-basho fibers.
Center: Taira Toshiko has been a central figure in passing on bashofu techniques to revive this tradition.
Upper right: Rolls of dried fibers called chingu ready to be made into thread.
Lower right: Weaving bashofu.