niponica is a web magazine that introduces modern Japan to people all over the world.
2013 No.11
To read the e-book you need to have JavaScript enabled in your browser and a free Flash Player plug-in from Adobe Systems Inc. installed.
Japanese Fabrics Have Their Global Reputation Wrapped Up

Japanese High-Tech Textiles Circle the World, and Beyond
The integration of centuries-old textile arts with cutting-edge scientific technology—both impressive in themselves—has given rise to high-tech Japanese fabrics that have made a powerful mark on global industry. These materials protect spectators at the racetrack and in the stadium from wind, rain, and blazing sun, and they also provide ecological solutions for greening barren land and mitigating water shortages. Japanese companies have found ways to mass-produce an "artificial spider silk" that is stronger than steel, and high-tech textiles developed in Japan are playing a major role on the frontiers of space exploration.
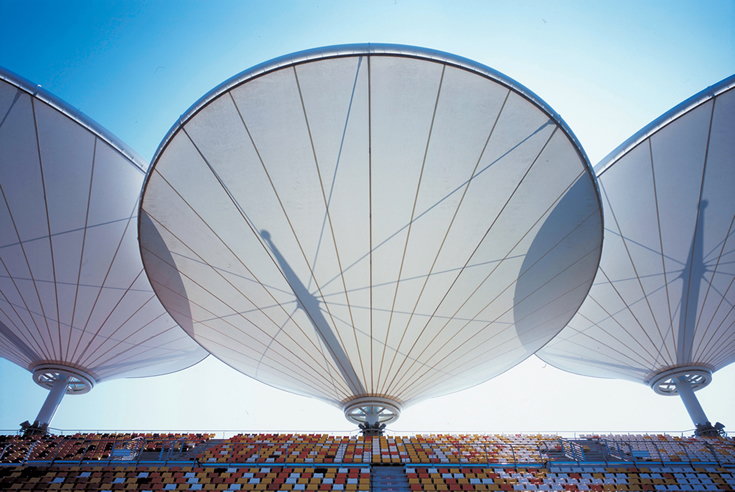
This grandstand at the Shanghai International Circuit racetrack is shaded by structures manufactured and installed by Taiyo Kogyo. (Photo courtesy of Taiyo Kogyo Corporation)
Japanese Tensile Membrane Adds Color to Major Architecture Worldwide
An hour by car from the center of Shanghai, massive "lotus leaves" float in the air above the Shanghai International Circuit. Twentysix of these tensile membrane roof structures shade the sub-stand seating for 20,000 spectators. Made of glass fiber coated in fluoroplastic, each leaf-shaped structure is an ellipse measuring 31.6m long and 27.6m wide and is held up by a steel frame pillar one meter in diameter. Evoking an image of overlapping lotus leaves floating placidly on the surface of a pond, this ultra-modern roof design employs technological expertise developed by Japanese companies for creating outstanding membrane structures.
As roofs, membrane structures are both lightweight and offer superior lighting, making them widely used for racetracks built without support columns, as well as large spaces with innovative architectural designs. Only a handful of companies, however, boast the expertise needed to produce this type of material. Creating complicated, three-dimensional tensile membrane structures requires extremely advanced techniques both in the manufacture of the cloth and on-site execution of the design.
The Arena Fonte Nova Soccer Stadium opened in April 2013 in the port city of Salvador on the Atlantic coast in northeastern Brazil. It seats 56,500 people and features a tensile membrane roof structure manufactured by the same company that created the "lotus leaves" for the Shanghai racetrack. The roof will shelter the seats at the Arena Fonte Nova when it hosts a quarterfinal match in the soccer World Cup to be held in Brazil in 2014.

Taiyo Kogyo also manufactured and installed the roof for the Arena Fonte Nova in Brazil. (Photo courtesy of Taiyo Kogyo Corporation)
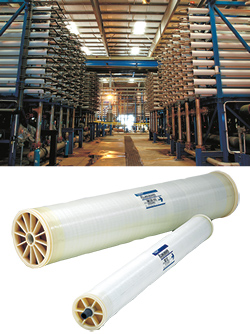
Ocean water desalination plant in Trinidad and Tobago uses reverse osmotic membrane elements manufactured by Toray. (Photo courtesy of Toray Industries, Inc.)
Life-Sustaining Plant Turns Seawater into Drinking Water
Completely surrounded by ocean, the Caribbean islands of Trinidad and Tobago have struggled for many years with a chronic lack of drinking water. Today, a life-sustaining plant turns saltwater into drinking water, playing a vital role in the lives of the residents here. With a massive processing capacity of 136,000m3 a day, this is one of the largest desalination plants in the world.
The heart of the plant is a reverse osmosis membrane supplied by a Japanese manufacturer. Using macromolecular technology, tiny holes no more than a few nanometers in diameter allow only water molecules to pass through the membrane, keeping salt out. Equipped with 20,000 reverse osmotic membrane elements manufactured as industrial products, this plant desalinates ocean water to supply residents with drinking water.
Fresh water that people can actually drink accounts for only a small fraction of the planet's water, leaving most regions in the world struggling with a serious lack of water. Desalination plants capable of turning abundant ocean water resources into fresh potable water are contributing a great deal to resolving the global issue of water shortages.
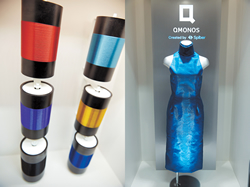
Colorful QMONOS thread, a fiber made of protein to resemble spider silk, and a dress created from QMONOS fabric (Photo courtesy of Spiber Inc.)
Dream Fiber Changes the World
The area around Tsuruoka in Yamagata Prefecture, otherwise a pastoral town in the Tohoku region and one of Japan's leading producers of rice, is the surprising home of one of the most cutting-edge man-made fibers in the world. Stronger than steel and more elastic than nylon, the "artificial spider silk" produced here meets the needs of an array of industries that need fibers that are light, yet strong. This includes materials for automotive parts, artificial blood vessels, and human hair, as well as thread for clothing.
Although a great many scientists had attempted to create artificial spider silk with these special properties, no one had been able to successfully mass-produce the manmade fiber—until a venture firm formed by a group of young researchers from Keio University came along. The startup utilized the latest biotechnology to enable a different organism to create a protein resembling spider silk. The scientists then collected this protein and processed it into fiber.
The experimental facilities for mass production will be completed in December 2013, and research and development is now being fast-tracked in anticipation of full-scale mass production within a few years.
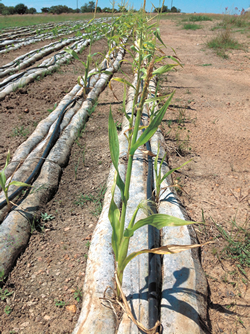
Roll planter tubes laid out on barren land in South Africa are produced using biodegradable fiber developed by Toray and knit manufacturing techniques developed by Mitsukawa of Fukui Prefecture. (Photo courtesy of Toray Industries, Inc.)
Textiles Restore Life to Barren Land
In the suburbs of Johannesburg, South Africa, farmers are working hard to reclaim land laid to waste by mining. Central to these efforts are long fabric tubes manufactured using a method jointly developed by Japanese knit and fiber manufacturers. Farmers fill the tubes with soil and fertilizer, lay them in long rows on the ground, and plant crop seeds between them. Before long, corn and other plants take root in the tubes, and the fields gradually expand. At the same time, the tubes also help keep wind from scattering sand in the air. Knit from biodegradable polylactic acid fiber that will decompose into soil, these tubes are produced using maruami, a circular knit technique developed by Japanese knit manufacturers for outstanding elasticity. The tubes are easy to set up, and they also retain a great deal of water. This superior water retention allows farmers to grow crops even with a small amount of water and fertilizer. People will now be able to grow crops in the desert—even on concrete, so the idea is attracting a lot of attention.
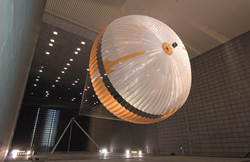
Space probe Curiosity's landing parachute deploys during a wind tunnel experiment. The suspension cords connecting the parachute and the space probe are made of an aramid fiber called Technora that was developed by Teijin Ltd. (Photo courtesy of NASA/JPL-Caltech)
Tough Fibers Stand the Rigorous Test of Outer Space
Venturing away from Earth, high-tech textiles travel to outer space.
The National Aeronautics and Space Administration (NASA) successfully landed the unmanned space probe Curiosity on Mars in August 2012. Once the space probe entered the Martian atmosphere, a massive parachute measuring 15m in diameter was released to slow its speed from 1,450km/h to 290km/h. The 80 suspension cords connecting the parachute and the probe were made out of another extraordinary fiber developed by a Japanese company.
These special aramid fibers have a tensile strength-to-weight ratio eight times greater than steel. This strength, in combination with a heat resistance enabling them to withstand temperatures of 200ºC for long periods of time, give these aramid fibers extraordinary properties that duly impressed the officials at NASA. According to NASA calculations, the parachute would be required to withstand a maximum gravitational pull nine times stronger than that on Earth during landing, and the 80 suspension cords would need to withstand a load of 27 tons.